1. Analysis of the prospect of frequency conversion of paper machine
The paper industry is one of the basic industries in China. The domestic pulp and paper enterprises are large and widely distributed, and occupy an important position in the entire national economy. It is one of the four major inventions in China. Papermaking machinery consists of raw material preparation, pulping, paper making, reels or flat sheets, and machinery for processing paper and paperboard.
According to statistics, China has more than 37.8 million tons of production capacity, single machine production capacity of more than 50,000 tons and more than one-third of the board machine production capacity of more than 100,000 tons, more than two-thirds of the production capacity needs Investing heavily in the transformation, at least one-third of the paper machines need to replace part or all of the original transmission parts (including mechanical gearbox and motor drive) to increase the speed and reduce energy consumption.
According to the estimated budget of installed power, it can be expected that about 300,000 kw of installed power will need to be converted in the next five years. According to the transformation system 1kw/1500 yuan, there will be about 450 million yuan of inverter market. Due to the domestic localization transformation project, a considerable number of domestic inverters will be adopted. Therefore, the market potential of domestic inverters is huge and should be Caused enough attention.
China's paper machine sub-section transmission equipment used SCR DC speed regulation method. Due to the existence of slip ring and carbon brush, the reliability and accuracy are not high, which leads to the backward performance of the paper machine. The maximum speed is only about 400m/min, which is difficult to compare with foreign countries. Compared to a 1000m/min high speed paper machine.
AC variable frequency speed control technology is recognized as one of the most promising AC speed control methods because of its excellent speed regulation performance, remarkable power saving and wide applicability in the national economy. It not only has the excellent speed regulation performance of DC motor, but also has the simplicity and reliability of AC motor, so it is gradually being widely used.
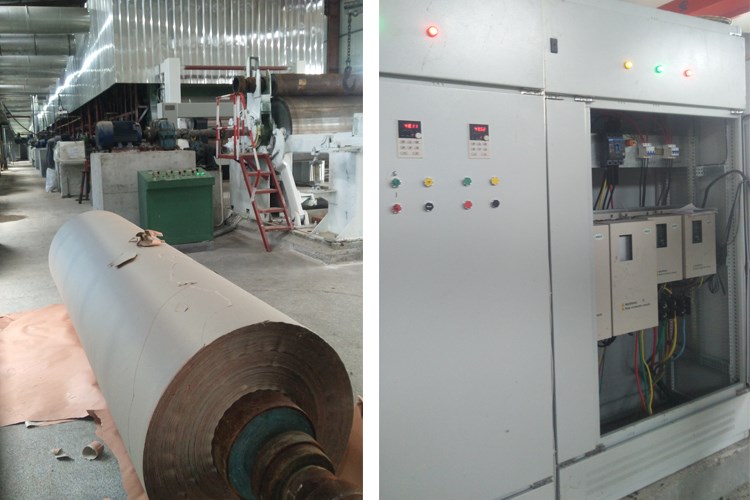
2. Energy-saving application of frequency converter in paper industry
Auxiliary facilities for paper machines include the following systems: slurry systems, white water systems, vacuum systems, compressed air systems, chemical preparation and transfer systems, water supply systems, steam systems, and the like. In order to enable the paper machine to operate continuously and evenly, its auxiliary facilities capacity should generally exceed 15% to 30% of the maximum capacity of the paper machine.
2.1. Frequency converter application of the slurry system
The slurry system must meet the following conditions:
(1) The slurry delivered to the paper machine should be stable, and the error should not exceed ± 5%;
(2) The ratio and concentration of the slurry should be stable and uniform;
(3) Reserve a certain amount of slurry so that the feeding capacity can be adjusted to adapt to the change of paper machine speed and variety;
(4) Purifying and selecting the slurry;
(5) Handling various parts of the paper machine.
Under normal circumstances, the slurry supply system consists of a slurry pump, a slurry pump and a pressure filter and a slag remover for the purification pipeline. To achieve the above five objectives, the most important thing is to use the slurry pump and the slurry pump. The full-speed operation is transformed into a variable-speed variable-frequency operation, which finally meets the automation of the slurry.
2.2. Frequency converter application for compressed air systems
Compressed air is commonly used in pneumatic pressurizing lifting devices for wire mesh and press sections of paper machines, correction devices for netkets, air-cushion headboxes, paper-feeding equipment, coated air knives, and various pneumatic instruments and adjustment devices. In the compressed air system, the main equipment includes air compressor, gas storage tank, pressure reducing valve, air filter, steam separator and safety valve. The pressure on the paper machine usually needs to be about 5~6 BAR. In most paper mills, more than two air compressors are operated in parallel, and then the gas tank is used to keep the pressure constant.
Since the compressor power is large and the control pressure is generally adjusted by loading or unloading, the motor is always running at full speed. Practice has shown that this control method consumes a lot of energy and wastes a lot. Therefore, it has been tended to use a single inverter control and multiple direct power frequency operation to control the compressor unit and form a pressure closed loop system.
2.3. Application of frequency converter for chemical preparation and transfer systems
Since a large amount of chemicals are used in deinking, pulping, coating, sizing, etc., the amount used is proportional to the speed of the multi-drive of the paper machine, so the chemical delivery system (such as a pump) must be used. Stepless AC speed control system, the preferred one is the frequency converter. Mainly based on the chemical pump power is relatively small, generally between 0.4kW ~ 5.5kW, and the performance price ratio of this power section of the inverter is already the best, electromagnetic speed regulation is still widely used many years ago And stepless speed gear pumps have been eliminated. According to the latest market statistics, the lowest-power inverters of medium brands have fallen below 1,000 yuan/kW.
A large number of grinding equipments are used in the preparation of chemicals, such as ball milling, colloid milling, sanding, high shear dispersion stirrers, etc. Their biggest features are high power, high energy consumption and harsh operating environment. At present, some manufacturers have achieved good results by using frequency converters on grinding equipment.
2.4, the application of the frequency converter ventilation system
In the drying section, all the water vapor evaporated from the paper is absorbed by the air and must be continuously removed from the papermaking plant by forced ventilation. The ventilation of the drying section is good or not, which directly affects the evaporation speed of the moisture in the paper sheet and the economy of the whole drying process; the ventilation is good, the steam saturation in the air can be reduced, thereby reducing the consumption of the steam in the drying cylinder and improving the drying. Dry speed. The amount of air necessary to remove the amount of water evaporated from the dryer section is related to the temperature and humidity of the incoming and outgoing air, as well as the ventilation system, weather conditions and seasons employed. Generally, in a modern paper machine, forced air circulation is used for high efficiency, and an air blower is used to feed dry air heated to about 80 degrees into the lower layer of the drying section, so that the hot steam is adsorbed between the drying cylinders to form an upward airflow. The hot and humid air collected in the hood is then taken out of the room by an exhaust fan (final waste heat is finally recovered). In high-speed paper machines, due to the increase in the number of dryers, it is usually divided into several sections of blowers and exhaust fans. After the inverter is used, the intake air amount (the speed of the blower) and the exhaust volume (the speed of the exhaust fan) can be adjusted at any time according to the expert calculation formula of the ventilation air volume, without the need of the traditional damper control, further reducing the energy consumption and reducing The noise of the fan improves the mechanical life.
2.5. Water system inverter application
The paper machine is a large water user, including white water system, sewage system, sealed water system, sprinkler system, water cleaning system, etc. Usually, the pipe network constant pressure water supply is needed, but the traditional pressure control is through bypass and The regulator is used for the valve and the inverter is rarely used. However, due to the general lack of water resources in China, the application of frequency converters will save 10% of water and 30% of energy, which will inevitably reduce the daily operating costs of paper mills.
3. Papermaking advantages after frequency conversion transformation:
