1. The necessity of servo casting of die casting machine
The full hydraulic die casting machine is a typical cyclic working equipment. It can be roughly divided into mold clamping, soup, shot, core pulling, mold opening, thimble, cooling, and storage in a complete working cycle (process process). Pressing several stages, each stage is to pump hydraulic oil through the oil pump motor to each cylinder to drive the transmission mechanism to complete a series of actions, each stage requires different pressure and flow. For the hydraulic system, the pressure and flow matching are different at each stage, and the power of the oil pump motor is configured according to the maximum load during its operation, while the die casting machine only has high pressure clamping and ramming work in one working cycle. The stage load is large, the other work stages are generally small, and the load during the cooling process is almost zero. For the oil pump motor, the die casting machine process is a variable load state. In the hydraulic system of the dosing pump, the oil pump motor provides a constant flow rate at a constant speed, and the pressure and flow rate required for the operation are based on the pressure proportional valve and The flow proportional valve is adjusted to control the pressure or flow rate by adjusting the opening of the pressure or flow proportional valve. Excess hydraulic oil is returned through the overflow valve. This process is called high pressure interception, and the energy loss caused by it is generally above 50%.
The traditional die-casting machine has higher oil temperature, higher noise, large leakage of hydraulic oil, high cost of electricity for the user, and troublesome maintenance. The inverter and the conventional die-casting machine can save part of the electricity, but the disadvantages of the quantitative pump part can not be avoided. In the past, the main energy-saving retrofit technology was frequency conversion energy-saving technology, but the frequency conversion energy-saving technology still had its obvious defects.
First, the inverter control accuracy is very low, and the direct output will cause the pressure and flow accuracy to fail to meet the machine requirements. Therefore, each output must pass the pressure and flow of the PQ valve overflow control system, which inevitably causes energy waste. .
Second, the motor is still an ordinary three-phase asynchronous motor, and its efficiency and power factor are lower than the current permanent magnet synchronous servo motor, especially when the load is clear, the difference between the two is more obvious. General statistics show that under the average working condition of the die casting machine, the total efficiency of the servo motor (including the driver) is about 10% higher than that of the asynchronous motor.
Third, for ordinary asynchronous motors, the starting and overloading operations generally require 5-7 times of current to output 2 times of rated torque, while the servo motor only needs 2 times of rated torque at rated speed. Double supply current.
Fourth, due to the motor response speed limitation during variable frequency control, the production efficiency of the equipment is reduced.
'Energy-saving' die-casting machines have become an urgent need to pay attention to and solve problems.
2. Characteristics of electro-hydraulic servo
The electro-hydraulic servo system consists of a host computer, a servo drive, a servo motor and an oil pump. The servo motor automatically matches and adjusts the energy requirements of the device. The PID algorithm is used to control the servo drive through the bus interface.
Compared with the traditional variable pump system: inverter + asynchronous motor, inverter + servo motor and other systems have the following advantages:
A. The response speed is fast - the response time of the servo injection molding machine can reach 0.025s (0-maximum output), which is obviously faster than the traditional hydraulic power control system, which effectively shortens the cycle and improves the production efficiency;
B. Significant energy saving - The output power of the servo oil press changes with the load, and there is no waste of excess energy. The servo motor in the accumulating stage reduces the speed, the energy consumption is extremely low, and the motor does not work during the cooling phase, and the power consumption is 0. Depending on the product, the servo-casting machine can save 40%~80% of electricity compared with the traditional die-casting machine. You bring real power-saving enjoyment and significant economic benefits;
C. High control precision - the repeatability of the servo injection molding machine system can reach 3‰, which is higher than the traditional hydraulic pressure control system, which ensures the stability of the product, reduces the rate of defective products, and greatly improves the qualified. Product rate
D. The system noise is smaller;
E. Higher production efficiency (can run at constant power and overspeed);
F. Compared with the traditional system, the motor power of the same tonnage equipment can be smaller, the installation space is small, and the equipment grade is improved;
3. System wiring and scene pictures

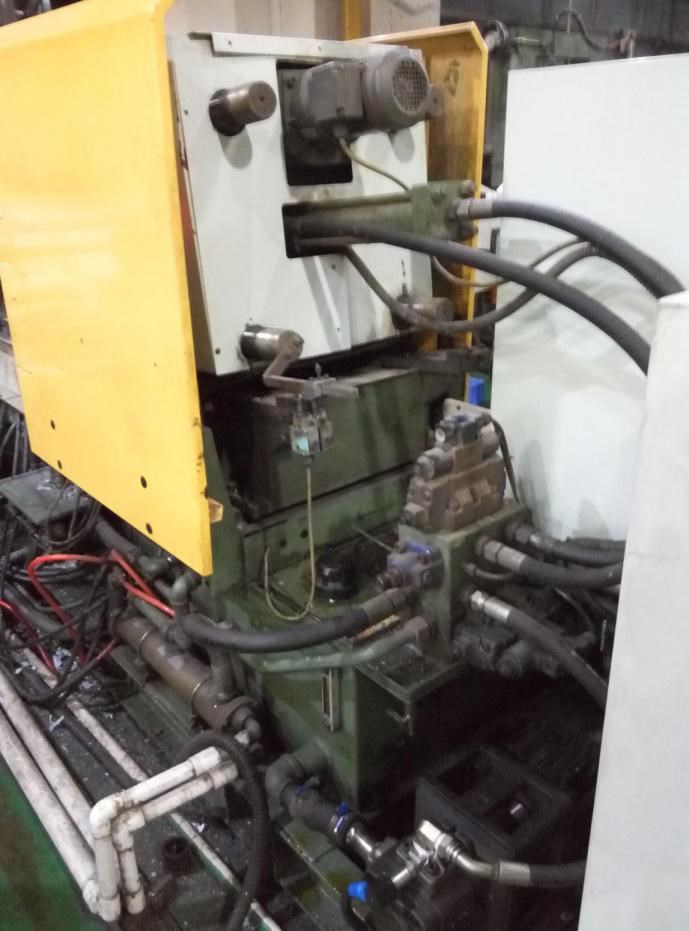

4. Summary
The SINCR SD500 electro-hydraulic servo system can detect the pressure and flow signals from the hydraulic system of the hydraulic press in real time, adjust the speed of the motor required for each working condition in real time, and let the flow and pressure of the pump output meet the needs of the system, while in the non-operating state. When the motor is running at a low speed, how much is actually given, and the energy saving space is huge. The site originally used a 22KW asynchronous motor, which consumes 18 degrees of electricity per hour. After the servo energy-saving retrofit, the energy consumption per hour is 6 degrees and the power saving rate is about 60%. Under the premise of satisfying customer performance and stability, SD500 electro-hydraulic servo system perfectly solves the requirements of cost, efficiency, oil temperature and precision of customers. Electro-hydraulic servo drive technology is the development direction of future die casting machines.