Summary
SINCR C500 series inverters help Jinzhou a wire drawing machine on-site production of two production lines, one 22kw, eight 18.5kw, one 15kw, precise control, energy saving and efficiency.
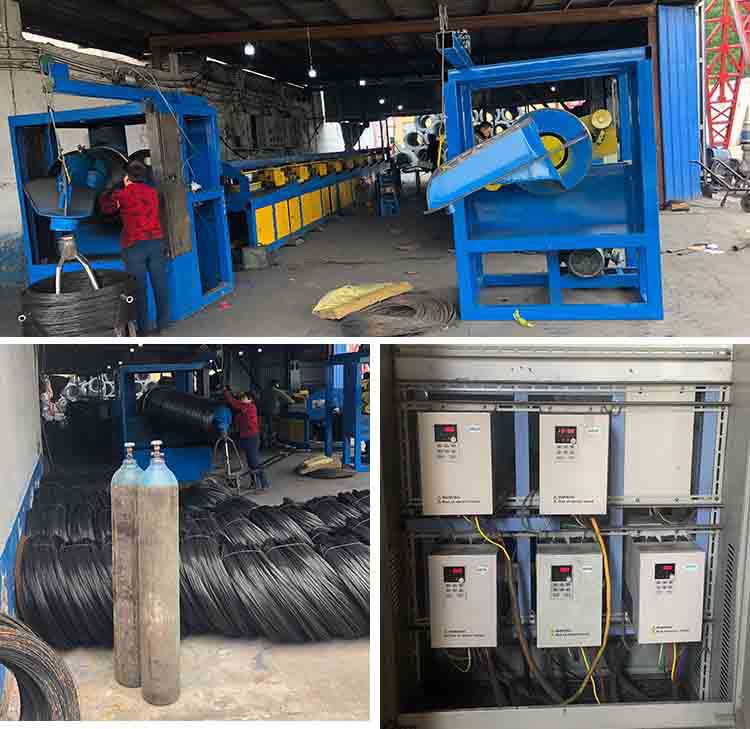
Introduction
The wire drawing machine is an important equipment for the production of metal wire, mainly for drawing metal wire into various specifications of filament. From the product specifications can be divided into: large pull machine, medium pull machine, small pull machine and fine pull. From the mechanical structure can be divided into: pulley type, loop type, water tank type and straight type. In the wire and cable industry, dual-conversion fine-pull applications are widely used. Relatively speaking, the required control performance is also low, and for most steel wire manufacturers, the precision requirements and the drawing stability are high for the material properties, so there are many straight-through wire drawing machines. In particular, welding consumables manufacturers, gas shielded welding wire, submerged arc welding wire, aluminum welding wire, argon arc welding wire, stainless steel welding wire, high strength welding wire and the most advanced flux cored wire have high requirements for electrical control of wire drawing machine. As the main electrical control part, the performance of the frequency converter, especially the precision of the tension control, directly affects the quality and output of the product.
First, the process needs
1, wearing a mold
Before starting the whole machine, the front end of the raw material must be manually polished and passed through the mold step by step. At the scene, the motor is usually driven by the foot switch to achieve low-speed rotation. At the same time, the wire is pulled from the front end of the mold to the rear end by the tool. The thread passing through the mold is first to be ground or pulled in order to pass the next mold. Fine, before you can pass the next level of mold. In this process, the motor is required to have a large and stable torque at start-up and low-speed operation, the running speed is stable, and the motor is not reversed during the deceleration stop.
2, drawing
After the mold is finished by hand, the whole machine can be run to achieve continuous stretching. The straight-through wire drawing machine is usually controlled by a plurality of motors, and after a plurality of drawing dies, the raw materials are pulled to the finished product of the required wire diameter at one time. In this process, the motor is required to respond quickly, the tension of the wire is constant, the tension of the tension balance bar is small, and the wire is not loose.
3, winding up
The winding part is driven by a separate motor, and the stretched finished product needs to be wound on the spool in synchronization. As the wire wound on the spool is thicker and thicker, the motor speed is correspondingly slower. When the thickness of the winding reaches the set value, the system provides automatic detection and shutdown. In the whole process, whether it is start acceleration, stop deceleration or stable constant speed, the line speed of the winding motor and the front end motor is required to be synchronized, and the wire is not loose, requiring the winding motor to respond quickly and speed. Control is precise.
4, cable
Usually, the finished wire is layered on the spool. On the horizontal axis of the spool, the wires should be arranged in parallel and tightly one turn. In this process, a wire arranging device is required to complete the alignment of the wire at the upper end to the lower end of the horizontal axis. The speed at which the wire arranging device reciprocates can be constant speed or controlled according to the speed of the winding motor. According to the requirements of mechanical design, there are many ways to realize the cable, such as mechanical and frequency conversion.
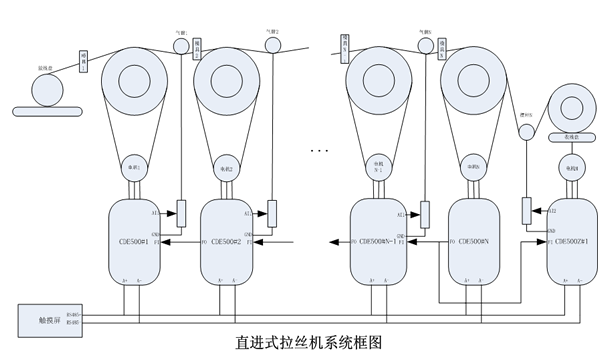