1.Introduction
Central air-conditioning is one of the indispensable supporting facilities for modern large-scale buildings. According to statistics, the consumption of electric energy accounts for about 50% of the total consumption of buildings. The central air conditioning system is designed to increase the load by 10% to 20% according to the maximum load. Due to seasonal, day and night and user load changes, the actual load is much smaller than the design load, and the full load running time is less than 1%. Although the load of the central air-conditioning main unit can automatically adjust the load with seasonal temperature changes, the system-matched refrigerating pump, cooling pump and cooling tower fan can not automatically adjust the load, and operate under 100% load for a long time, resulting in great energy. Waste, with a lot of energy saving space.
2. Central air conditioning system
Figure 1 shows a typical central air conditioning system diagram, which consists of a chilled water circulation system, a cooling water circulation system and a refrigeration mainframe:
2.1, chilled water circulation system
This part mainly consists of chilled water pump, terminal fan unit and chilled water pipeline. The low-temperature chilled water flowing out of the main evaporator is pressurized by a refrigerating pump and sent to the chilled water pipe, enters the room for heat exchange, takes away the heat in the room, and finally returns to the main evaporator. Indoor fan cabinets are used to blow air through chilled water pipes, reducing air temperature and accelerating indoor heat exchange.
2.2, cooling water circulation system
This part is composed of a cooling pump, a cooling water pipe, and a cooling water tower. While the chilled water circulation system performs indoor heat exchange, it will take away a lot of heat energy in the room. The heat is transferred to the cooling water through the refrigerant in the main unit to raise the temperature of the cooling water. The cooling pump presses the heated cooling water into the cooling tower to exchange heat with the atmosphere.
2.3, cooling host
The central air-conditioning main unit is composed of a refrigeration compressor, an evaporator, a condenser, a throttle valve and a refrigerant. The working cycle is: first, the low-temperature and low-pressure gaseous refrigerant is pressurized by the compressor into a high-temperature and high-pressure liquid, and is cooled in the condenser. The circulating water is cooled and released to the atmosphere through an outdoor cooling tower. Subsequently, the throttle valve is throttled and reduced to become a low-pressure gas-liquid mixture and enters the evaporator. The refrigerant is continuously vaporized in the evaporator, and the heat in the refrigerating circulating water is absorbed to form cold water. Finally, the vaporized vapor in the evaporator becomes a low-pressure gas, re-entering the compressor, and so on.
3. Central air conditioning energy saving theory
According to the theory of fluid mechanics, the output flow Q of a centrifugal fluid transmission device (such as a centrifugal water pump, a fan, etc.) is proportional to its rotational speed n; the output pressure P (head) is proportional to the square of its rotational speed n; the output power N and its rotational speed n The cube is proportional to the mathematical formula, which can be expressed as:
Q=K1×n
P=K2×n2
N=P×Q =K3×n3 (K1 K2 K3 is a proportional constant)
It can be known from the above principle that the variable frequency stepless speed regulation technology is used to control the speed of the water pump to adjust the flow rate. When the flow rate decreases, the power consumption will decrease in the ratio of the cubic. If the power supply frequency of the motor is reduced from 50 Hz to 40 Hz, theoretically, the power consumption will be reduced by 48.8%.
4. Central air conditioning renovation program
4.1. Control scheme for circulating water system
The chilled water circulation system adopts a stable temperature difference (the real-time adjustment of the output frequency of the inverter according to the cooling capacity to stabilize the temperature difference), the pressure difference (guaranteeing the maximum cooling pressure to meet the requirements) and other parameters control; the cooling water circulation system uses a stable temperature difference, and the cooling tower Parameter control such as ambient temperature and humidity, temperature difference of cooling system and environmental temperature and humidity control, the performance of the host is obviously better than the cooling water outlet temperature control. The temperature difference between the inlet and outlet of the freezing and cooling water is controlled at 4.5~5°C. The feedback signal of the control system according to the load changes is adjusted by the PID and the frequency converter forms a closed-loop control system. The PLC controls the working frequency of the inverter and the number of pumps running according to the monitoring value. Thereby adjusting the circulating water flow rate and controlling the speed of heat exchange of the central air conditioning system.
4.2, cooling tower cooling system control program
The cooling tower cooling system temperature sensor detects the cooling tower outlet water temperature value, and controls the cooling tower outlet water temperature to 27 to 29 ° C. The PLC controls the number of cooling tower fan operating units and the operating frequency of the frequency converter according to the outlet water temperature, so that the cooling water outlet temperature reaches the setting. Value.
4.3, electrical control program
The data of the central air conditioning unit of a building is as follows:
Before the transformation, the power frequency operation, the average temperature difference between the freezing and cooling inlet and outlet water is about 3.5 °C, and the smaller the temperature difference is, the larger the energy saving space is.
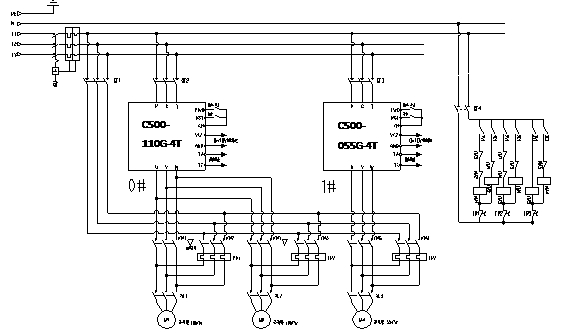
5. Advantages of frequency conversion transformation of central air conditioning system
5.1, using inverter closed-loop control, software configuration can be carried out as needed and the temperature is set for PID adjustment, so that the output power of the motor changes with the change of the heat load, and the maximum energy saving can be achieved under the premise of meeting the requirements of use;
5.2. The frequency converter has soft start and soft stop, which reduces vibration, noise and wear, prolongs the maintenance period and service life of the equipment, reduces the impact on the power grid and improves the reliability of the system;
5.3. The inverter has many protection measures such as overvoltage, undervoltage, overcurrent and grounding to the motor, which greatly improves the operation rate and safety reliability of the system;
5.4. The isolation effect of the DC capacitor in the inverter makes the input power factor close to 1, and the excitation reactive current of the motor is provided by the capacitor, which can save the power grid capacity;
5.5. The variable frequency speed control closed-loop control system and the original power frequency control system are interlocked with each other, which does not affect the operation of the original system. When the variable frequency speed control closed-loop control system is overhauled or faulty, the original power frequency control system can still operate normally.
6. Summary
SINCR Electric C500 series inverter is applied to the central air conditioning system. It adopts variable frequency closed-loop control motor to set the temperature as needed, so that the equipment reserve capacity and the thermal load over time can be adjusted by the speed to achieve maximum energy saving when the requirements are met. At present, it has been successfully applied to a number of central air-conditioning energy-saving renovation sites. According to statistics, the average power-saving rate has reached more than 30%.