1. Introduction
The injection molding process is generally divided into the following steps: mold clamping → injection holding pressure → melt rubber feeding → cooling setting → mold opening thimble. The completion of each action has a precise fit of several parameters such as time, pressure, speed, position, etc., that is, the displacement at a certain position has a corresponding pressure and speed, and the pressure and the pressure in different positions and times The speed is variable. At the same time, after each action is completed, a termination signal is sent to the program controller, and the program controller receives the signal and then issues an instruction to perform the next action. In addition, the injection molding machine system itself has some weaknesses:
(1) There is a very violent mutation process inside the injection molding machine: in the process of clamping, rapid mode-locking → slow low-pressure protection → high-speed high-speed clamping is a very sudden change in the working conditions; Injection → fast → slow → fast → slow
The working condition of the injection molding process is also very severe, and the impact on the machine is very large, which affects the life of the entire injection molding system.
(2) The action oil circuit brake can not reach the design accuracy, the oil circuit brake opening and closing depends on the solenoid valve, and the action of the solenoid valve depends on the voltage and current supplied by the process controller, because most injection molding machines are Without the endless loop control, the valve opening and closing accuracy will be greatly reduced, especially when the valve opening and closing degree is below 10% and above 90%, an action is executed in this state.
It is difficult to guarantee its stability and repeatability.
(3) The oil cylinder that performs the action itself has oil seal damage and internal leakage, and the reliability and stability of the execution action are not high. This is because most of the time, the actual fuel consumption of the load is less than the oil supply of the oil pump, causing the hydraulic oil in the high pressure state to overflow through the hydraulic components such as the relief valve and the proportional valve. The overflow portion not only does not perform any useful work, but also generates heat, causing the hydraulic oil to generate heat, which is both energy consuming and harmful. The frequency conversion operation of the injection molding machine can solve these problems well, which not only improves the accuracy and stability of the entire injection molding system, reduces the huge mechanical impact, prolongs the service life of the system, but also saves a lot of electric energy.
2. Injection molding machine frequency conversion energy saving principle
For the plastic products industry, electricity consumption is the main part of its production cost, and injection molding machine is one of the main energy-consuming equipment of plastic products factory. Therefore, reducing the energy consumption of injection molding machine has become the cost reduction of the injection molding industry and the competitiveness of products. Effective Ways. The traditional injection molding machine uses a fixed pump to supply oil. The various actions of the injection molding process have different requirements on speed and pressure. It uses the proportional valve of the injection molding machine to use the overflow adjustment method to bypass the excess oil back to the fuel tank. In the whole process, the rotation speed of the motor is constant, so the oil supply amount is also fixed, and since the execution action is intermittent, it is not possible to be full load.
Therefore, there is a lot of wasted space for quantitative oil supply, according to the actual measurement of at least 50%. Frequency conversion energy saving is aimed at this.
Waste space, real-time detection of proportional pressure and proportional flow signals from the CNC system of the injection molding machine, timely adjustment of various working conditions.
Make the required motor speed (ie, flow regulation), so that the pumping flow and pressure can just meet the needs of the system, but in the non-moving.
When the state is in the state (mainly in the cooling state), the motor is stopped, so that the energy saving space is further increased, so the note is
The transformation of the plastic machine with energy-saving energy conversion can bring huge energy-saving effects.
3. SINCR C500 vector inverter is applied to the energy-saving transformation of injection molding machine
(1) Acquisition of signals. The running start signal of the inverter takes the action execution signal of the injection molding machine computer; the speed control signal of the inverter takes the pressure proportional valve analog signal (0-1A) of the injection molding machine. After being processed by the inverter, each action corresponds to the corresponding frequency, and the oil pump oil speed is automatically adjusted to achieve energy saving purposes.
(2) Close the relief valve. The relief valve is used to adjust the system pressure when the motor is not controlled by the inverter. When the inverter is controlled, it should be turned off to achieve the best energy saving effect.
(3) The new Corey C500 vector inverter has fast response speed (acceleration/deceleration time of about 0.5s) and complete protection functions (over 30 kinds of protections such as overcurrent, overvoltage and overheat).
4. Problems and treatments that often occur during debugging
4.1 Precautions before commissioning
Injection molding machine frequency conversion energy-saving electrical transformation is relatively simple, but before the transformation should be detailed to understand the injection molding machine working conditions, familiar with the injection molding machine process, the following matters should be noted during commissioning: check the original circuit wiring of the injection molding machine before installation, including the main circuit And the control circuit; carefully observe whether the power frequency operation of the injection molding machine is normal, whether the oil pump motor is often in an overload state; observe the potential of the energy-saving transformation of the injection molding machine according to the mold and injection molding process of the injection molding machine; The signal line and the main return line should be separately routed.
4.2 debugging common problems and treatment methods
Due to the special nature of the injection molding machine process, various failures will be encountered in the transformation. The following are the problems and treatment methods often encountered in the frequency conversion transformation of injection molding machines.
(1) There is no change in the frequency of the inverter
Since the frequency converter adopts the valve control current signal of the injection molding machine to adjust the speed, the frequency display shows that the frequency is 0.0 (some inverters show 0), the main reason is that the signal polarity is reversed; the signal is wrong; the signal wiring The port does not match the parameter setting; the auxiliary power supply of the injection molding machine is faulty. If such a fault occurs, it should be first checked whether the type of valve control of the injection molding machine is a current signal, a voltage signal or a pulse control signal (some models), and the positive and negative polarity of the signal. Whether it corresponds to the inverter control terminal.
(2) The oil pump is noisy
After the inverter is running, some injection molding machines will generate abnormal noise. At this time, it should be judged whether the noise source is from the motor or the oil pump. If the noise of the oil pump is due to the following: the injection molding machine has too little hydraulic oil, and there is air inhalation; The oil filter or oil circuit is blocked; the oil pump blade of the injection molding machine is worn more seriously; if it is encountered, the injection pump oil oil pump should be inspected first, and the oil pump can be operated after the fault is removed. In addition, when the injection molding is in the low speed and high pressure working state, the oil pump noise will also be abnormal. In this case, the speed signal is appropriately increased.
(3) Temperature control interference
The problem often encountered in the transformation of injection molding machine inverter is that the injection molding machine can not operate normally after the transformation. The heating unit of the injection molding machine uses the thermocouple to detect the temperature. This detection component is easily interfered by harmonics, which causes the temperature display and control of the injection molding machine to be inaccurate. At this time, the interference can be eliminated from the following aspects: the wiring between the inverter and the motor of the injection molding machine should be shortened as much as possible, the metal hose set of the power line should be used, and the power line and the temperature detection line should not be close to the trace; the main circuit of the near end of the inverter The cable is equipped with a reactor or a magnetic ring; the inverter is reliably grounded; or the internal temperature-controlled galvanic power supply of the injection molding machine is coupled with a RC filter circuit, as shown in the following figure.
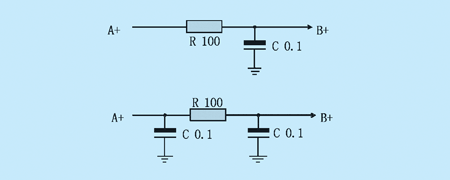
Injection molding machine temperature interference filter circuit diagram
Where a+ is the thermocouple end; b+ is connected to the temperature control board, and the above resistance and capacitance components are symmetrically added in the temperature detection (thermocouple) line during processing to eliminate interference.